
Resources, plastic granulate included, become ever more valuable. With the use of a cold runner system there are inevitably high costs due to the unusable sprue. It is precisely these costs that must be avoided for more efficient production. Using a hot runner system saves on the cost of the unusable material. You can use our sprue cost calculator to calculate how much material costs could be saved in the injection moulding process.
Sprue cost calculator
Other advantages of a hot runner system
Scarcity of raw materials and price increases in plastic granulate impact considerably on efficiency in production. By using a hot runner system, decisive application advantages can be achieved that have a positive impact on productivity. Although hot runners are often associated with higher procurement costs, there are many other technical and financial aspects that make them preferable to cold runners.
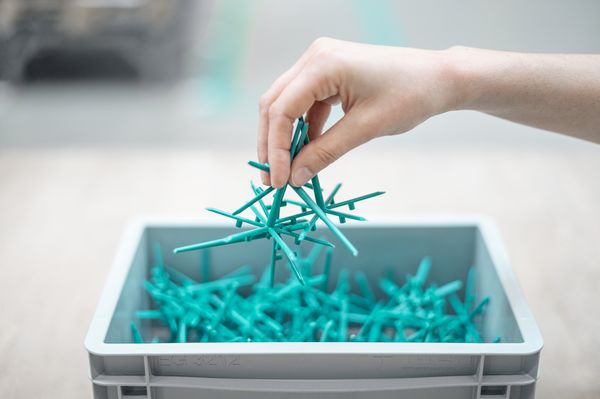
Technical perspective
- Shorter cycle times, as sprues usually have to cool down for longer
- Reduced loss of pressure
- Improved holding pressure effect
- Positive impact on shrinkage and warping
- Injection from the inside possible
- Potential to use stack moulds
Financial perspective
- No sorting of runners required
- No storage of runners required
- No regranulation required
- Less space required for the same production volume
Further information
If the advantages of a hot runner system outweigh the disadvantages for you, contact us and send us an enquiry. Our team is at your service. Alternatively you can also test our configurator for standardised hot runner systems.